|
by Alison Ruzsa & Sami Harawi
June 2005
Glass is an art medium with seemingly
endless technical versatility and a rich, long history. Basic elements
of sand and soda lime are combined with coloring agents, then melted
together to produce the raw material. The raw (soft) glass prepared in
Murano, Italy, has a great reputation anchored in centuries of
appreciation for its high quality. Although this well deserved
reputation persists today, good quality glass is produced elsewhere,
particularly in the United States
(Corning, Bull’s Eye and Schott glass).
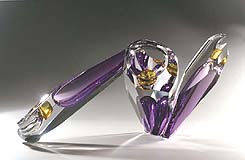
This essay will attempt
to clarify technical glass jargon and to describe in simple terms the
commonly used glass art techniques. Most of those are illustrated in the
sculpted letters created by the artists participating in
The
ABC of Glass Art.
References to images of their work are throughout the text.
No one knows exactly where and when experimenting with
Blown Glass,
began. The earliest examples are circa 100 BC. The technique spread
rapidly across the Roman Empire early in the Common Era. Although glass
blowing has reached a high level of sophistication, very little of the
technique itself has changed since the early times. To create a blown
glass object, the molten glass is
gathered
from the furnace on the end of a long hollow metal tube, the
blowpipe.
At this stage the glass is typically around 2100 degrees (Fahrenheit),
and has the consistency of honey (it becomes very stiff at around 900
degrees). The glassblower puffs air through the blowpipe into the center
of the gather.
A variety of tools are then used to shape the glass to form. As the
glass cools it begins to stiffen and must be reheated to allow shaping
and reshaping. For these re-heats, the glassblower uses a smaller
furnace, the
glory hole (because of its
bright glow). The re-heats allow the artist to work on a piece for a
long time, shaping and blowing until the desired result is achieved.
When the piece is finished, it is placed in an oven, the
Kiln
for annealing.
Annealing
is the process of slowly cooling the glass to room temperature to
stabilize its delicate crystalline structure. The piece will crack if
heated or cooled too quickly. Annealing is not only for blown glass, it
is an integral part of most of the techniques described below.
Hot Sculpting
denotes a technique in which glass is
gathered from the furnace on the end of a
solid
metal rod called a
Puntil,
or Punty,
and shaped into a sculpture (Petro).
Incalmo
in Italian means graft. It is a process which involves blowing at least
two separate cylinders of glass and joining them together (grafting
them) at
the open end to create a Vessel or a sculpture composed of pieces with
different colors and or content.
Cast Glass
predates blown glass.
The first casting technique, core-formed, is as old as glass itself. It
dates back to 2500 BC when bead work
started in Mesopotamian and was
followed by small core-formed vessels. Scholars believe that glass was
originally a by product of fine silver smelting and this by product was
used first as a ceramic glaze.
Core-formed Glass
technique consists in applying heated glass rods and murrine to the
outer
part of a mold (Matsushima). Today a wide range of techniques are used
to cast glass. Pate de Verre (French for paste of glass) and Kiln
Casting are similar. Both involve filling a mold with glass particles,
then heating it in a kiln till the glass fuses together at the melting
point. In
Pate de Verre (del Maestro' cast
hand, i below) the glass is crushed into a fine paste before it is put
in the mold. For
Kiln Casting
(King's Y, below), chunks of glass are used. Carl van Hees has used
specially prepared granulated glass (C below).
In
Hot
Casting
(Zimmermann, below right), glass is heated at a temperature higher than
for blowing glass (around 2350 degrees Fahrenheit). It is scooped out of
the furnace with large ladles and poured into a mold. Usually, the molds
are made of ceramic and silica, materials that withstand very high
temperatures.
Lost
Wax is a
method similar to bronze casting (Barney and O’Dorisio). The positive is
carved from a wax block. A plaster mold is then built around it. The wax
is melted out and the mold refilled with molten glass then fired in the
kiln.
Subtraction casting consists of
carving out a shape from a solid cast glass block (like carving a
stone). This technique is carried to a very interesting level by Alex
Bernstein. The color in Alex’s abstract sculptures comes from the glass
itself (below left), or from applying metal dust that results in a
rusted look.
Sand Casting is an ancient
technique. It involves creating a mold by depressing objects into silica
sand (which is mixed with a binder and / or injected with C02 to make it
hard). Molten glass is poured into the mold.
Optic Glass
(Janacek, below center) is the glass
that is cut in geometric forms then polished. It can start as blocks of
glass (from a company like Schott glass), or cast by the artist, then
polished.
Slumping & Fusing
are techniques that use flat pieces of (usually colored) glass (similar
to the glass used by stained glass artists), manufactured with specific
coefficients of expansion to make them compatible for melting together.
In
Fusing,
multiple pieces are arranged in a pattern and heated in a kiln (Krage).
In Slumping,
the glass is laid into, or on top of a mold and heated just to the point
where it “slumps” or moves with gravity when it becomes fluid with the
heat, to fit the form of the mold (Kanda). Once the glass reaches the
desired form it is cooled quickly enough to stop the movement but slow
enough not to destroy the crystalline structure (del Maestro and Heyd).
Although these methods sound simple, the objects created often have
intricate designs. Hours of painstaking labor may go into the
arrangement of the glass. Many of these pieces require multiple firings
in the oven to achieve the desired results. |