Mario & Antonio Dei Rossi Their
Technique
A Visit to the Dei
Rossis
There are two Cold phases and
a Hot phase in the creation of a Murrina
INITIAL
COLD WORK. The photo on the right shows Mario
preparing a Van Gogh self Portrait. The image of Van Gogh is
on the desk to his left; and the same image is in the box
facing him. He is placing flat thin glass rods (1/16 - 1/8”
wide and 2.5 - 3” long) against the image of Van Gogh in the
box. He matches the glass rod colors with the colors in the
image. This results in a cold piece similar to the “cold
cylinder” of Antonio’s Rooster, top right corner of this
page. It takes, an average of one month to complete the cold
work on a piece. A complex piece like the
Tempest may take six months.
Hot Work. The photo
on the left shows Antonio and Mario in the furnace. The
“cold cylinder” is heated according to a preset
schedule
with different temperatures at the different stages of the
process. The softened glass cylinder is then pulled as a
thick Rod. The heating and the pulling of the Rod are
the most delicate stages of the creation of a Murrina (read
A Visit to the Dei
Rossis
below). The rod is annealed,
to be readied for the last phase of the process.
FINAL COLD WORK. The
thick Rod is cut in cross sections as seen in the images on
the facing page. The cross sectioned pieces vary in diameter
and quality of the figure, depending on whether the Murrina
was cut from the central part or from the ends of the thick
Rod. The less perfect sections are discarded. |
|
|
|
|
The “cold”
stages of a Murrina |
|
|
|
|
|
The murrina of
Antonio’s Rooster on the left was made from the
Cold Worked cylinder on the right. Bundles of thin glass
rods are held together by metal wires (the ends of which
is seen at the10:00 position). The resulting cylinder is
3-4” in diameter and 2-3” high. In every piece, a 3/16”
signature rod is placed among the thin rods. That
of Antonio’s, ADR, is seen at the 4:00 position
in the
Rooster
Murrina (top left). Mario’s signature, MdR, is
obvious in the
Caravaggio Murrina. |
|
|
|
|
|
The thick Rods
that result from heating then pulling the “cold
cylinder” are shown below. The sectioned Murrini
are Antonio’s Butterfly, Parrot and Peacock Head. Most
of the murrini are 5/8-1” in diameter and 1/16’ thick.
The measurements of the few larger ones are indicated
within the Catalogue (e.g.
Parisienne
Japonaise) |
|
|
|
|
|
The image of the
Peacock Heads shows the variability of the Murrini as
they are cut from different parts of the Rod. |
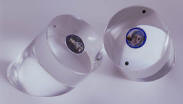
Plexiglas
Stands
3” diameter, 4 - 5.5” high
 |
|
A Visit to the Dei Rossis
In the Spring of 2003 we visited the Dei
Rossis in their home in Burano, and had the privilege to see the
two studios where Mario and Antonio do the Cold Work for the
Murrini. Antonio’s Orchid was ready as a “cold cylinder” of
bundled thin rods on the surface of which the Cattleya is seen in
a pattern similar to mosaic.
Two days later, we met them in a Murano Furnace and experienced a
thrilling couple of hours, in which the cylinder housing the
Orchid was transformed into a thick Rod of fused glass. During the
process, father and son were meticulously coordinating their
movements around the furnace in what we likened to the combined
elegance and risk of the acrobats in a Cirque du Soleil duet. Our
fear was related to mishaps that can happen along the elaborate
“hot process”: the risk of over fusing the image (resulting in its
distortion), of breaking the glass during one of its frequent
trips in and out of the oven, or the breakage risk in the
annealing phase. It happened to Antonio’s
Lion, and that is why
few good pieces are available of this superb Murrina.
All went seamlessly that Saturday, and the resulting
Cattleya Orchid is
beautiful. We left Murano that day even more amazed by these
miniature masterpieces than we first saw them at the time that
Cesare Toffolo offered us the first Dei Rossi Murrina few years earlier.
Sami Harawi & Charlie Reinhardt, July 2003 |
|
|